The kitchen serves as the focal point of every household. As a new homeowner, the top priority on your interior design checklist is a modern and efficient modular kitchen. With a reputation for being the most practical and stylish solution for your kitchen needs, choosing the right materials is essential for ensuring durability and cost-effectiveness. When it comes to modular kitchens, cabinets are typically composed of two parts: the skeleton or carcass, and the outer finish or exterior covering. In this post, we’ll delve into the specifics of kitchen cabinet materials, also referred to as the kitchen carcass.
1. Hardwood
Most of us have probably witnessed the presence of robust wooden cabinets in our childhood homes, or at least in the residences of our elders. These classic and durable cabinets are typically crafted from sheesham (Indian rosewood), teak, mahogany, or balut (oak). Interestingly, despite the evolution of kitchen styles, natural wooden cabinets remain a versatile option that complements both traditional and modern kitchens. Unfortunately, due to the increasing popularity of modular kitchens, the demand for natural wood has diminished considerably.
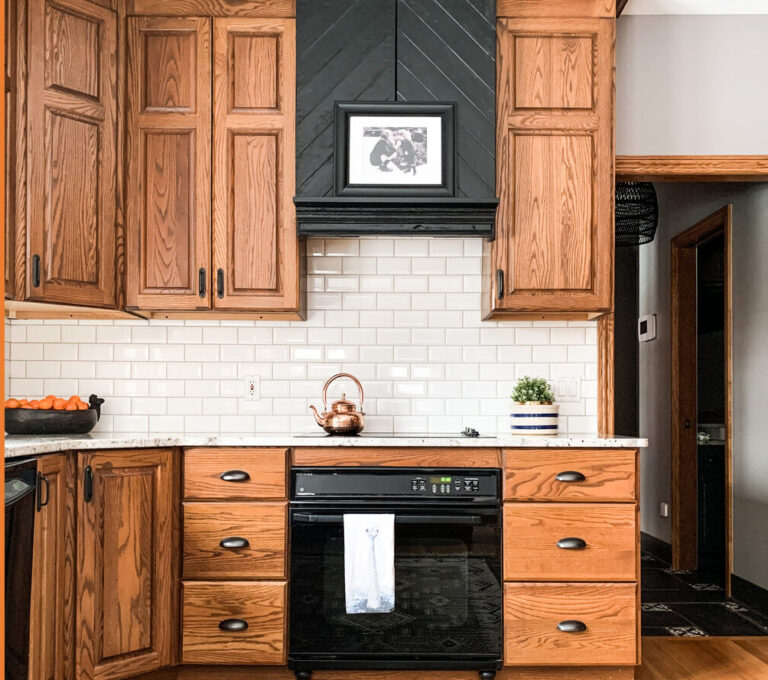
Pros:
- The textures and grains of natural wood are beautiful and the colours are deep.
- Wood is easy to maintain on a day-to-day basis, and you don’t have to worry about stains and spots. Just use a cloth to wipe clean! However, you will need to get the wood polished often to maintain the smooth texture.
- Wood is very strong and durable, and will last you many, many years — maybe even a lifetime.
Cons:
- Termites and other insects love wood, as much as we do. Therefore, it’s important that the wood is treated in advance.
- Moisture and humidity can affect the core of the material over time.
- Since it isn’t man-made and is now scarce, natural wood is much more expensive than any type of engineered wood.
- Takes a lot of time to produce a hard wood kitchen in comparison to the modular kitchens that are made in workshops.
2. Plywood (BWR Ply)
Plywood is a type of manufactured material or engineered wood that is produced by adhering multiple thin layers or veneers of wood together to form a single board. It is offered in varying thicknesses and exhibits considerable stability. To enhance its durability and shield it from potential harm by termites or moisture, it can be coated with plastic laminate, wood veneer, or thermofoil, resulting in a smoother finish. As modular kitchens become increasingly popular in India, plywood has emerged as the favored material, and it can be easily found in Indian markets today.
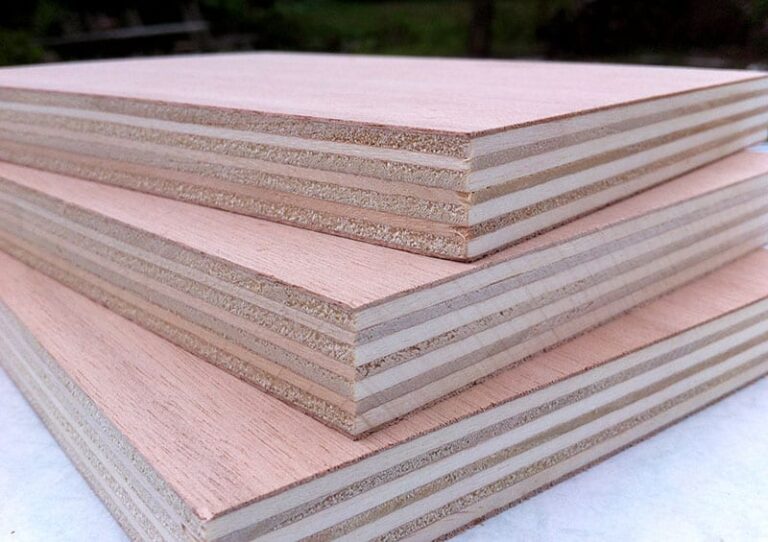
Pros:
- Plywood is less prone to damage by moisture or water — making it a great fit for Indian kitchens.
- Because of the way it is bonded (ie, with the grains running against one another), it doesn’t shrink, crack or warp. Hence, it is highly durable, too.
- It is affordable, costing anywhere between Rs. 85 and Rs. 115 per square foot for a 19mm-thick BWR plywood from a reputed brand like CenturyPly, Greenply or Kitply. The costs depend on the type and thickness of the board.
- It is stronger than all other engineered woods, and can better hold heavy weight.
- It is also lighter than other boards, and is, therefore, a great option for hanging or wall cabinets.
Cons:
- While it is much cheaper than solid wood, it is more expensive than HDF or MDF (read about these later in the article).
- Elaborate designs with plywood kitchen cabinets is difficult as the material is very dense.
- You have to ensure that your plywood cabinets are coated with laminate or veneer, so that the rough edges don’t show.
3. HDHMR
A relatively recent addition to the construction industry, HDHMR is a novel product that has gained popularity due to its exceptional features. HDHMR is manufactured by blending fibre chips and forest wood waste in a homogeneous process. During this process, the fibre chips are compressed into a single layer, removing small wood content to create a more robust, high-density board. The resulting product boasts superior density compared to other alternatives available in the market. The board has a consistent density gradient and a compact core, although the quality may vary depending on the brand. With its unparalleled quality and limitless applications, HDHMR is revolutionizing the Indian interiors industry by replacing traditional plywood.
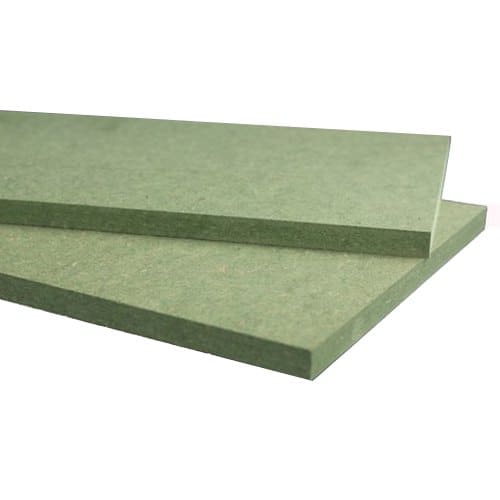
Pros:
- Tougher than plywood
- Highly water-resistant: Can be used in highly moist areas and climate
- Hard Wood used for higher density of product (made from eucalyptus wood)
- No Core Gaps – Ideal routable substrate with sharp cut & routed edges
- Uniform density gradient and Compact core – Enhanced screw and withdrawal strength
- Special Glue being used to make it Water Resistant Product as per Indian climate conditions.
- Ready & Smooth Surface – Polish with exotic colours of choices. Absorbs less paint in the painting process thus saves paint cost also.
- Innovative Application – Enhanced aesthetic value addition to finished product.
- Cost-Effective Paneling Solution
Cons:
- Costlier than plywood.
4. HDF & MDF
MDF stands for Medium-Density Fiberboard, while HDF stands for High-Density Fiberboard. Both MDF and HDF are engineered wood products made by breaking down hardwood or softwood residuals into wood fibers, which are then combined with wax and resin binders and pressed together under high temperature and pressure. The difference between the two is in the density of the fibers used. MDF has a medium-density fiber, whereas HDF has a higher density fiber. This results in HDF being denser and stronger than MDF.
MDF is often used for the carcass of kitchen cabinets because it has a smooth surface, making it ideal for laminating with veneers or painted finishes. It is also easy to cut and shape, which makes it suitable for creating intricate designs for cabinet doors or panels. HDF, on the other hand, is denser and stronger than MDF, making it a better choice for applications that require greater strength and durability, such as for kitchen drawers or shelving. HDF can withstand heavy loads and is more resistant to moisture than MDF, making it ideal for use in humid kitchen environments. Ultimately, the choice between MDF and HDF for kitchen carcasses depends on the specific requirements and design of the kitchen.
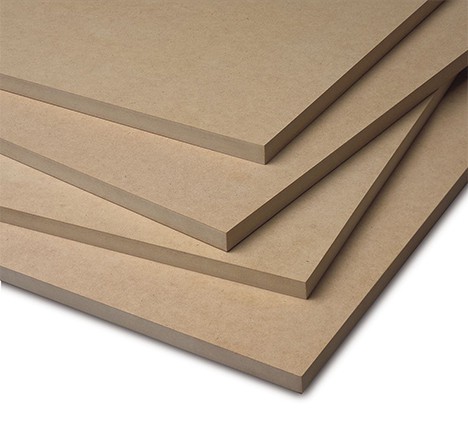
Pros:
- Both HDF and MDF have a very smooth surface (easier to paint), and can be easily cut for designs.
- They are a more economical choice (HDF is more expensive than MDF). Regular MDF would cost you less than plywood or HDHMR.
- Both are sustainable options as they’re made from fragments of wood leftover from projects or otherwise.
Cons:
- Since they’re denser (not stronger) than plywood, they’re heavier to work with. Plus, they’re not as strong as plywood.
- Both are not resistant to water or moisture and, hence, aren’t suitable for areas near the sink.
- They don’t hold screws well as they’re made of small grains and particles.